Want your teams to perform? Communicate well with them
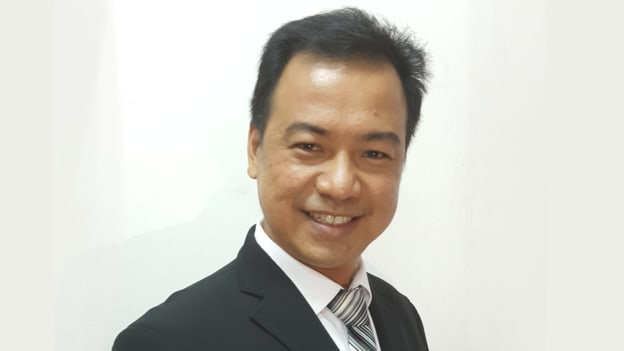
In manpower-intensive industries such as manufacturing, where many critical business operations cannot be carried out without employees on-site, performance and productivity have often skewed heavily towards bulking up the workforce. The shift towards automation can be slow and uneven, given the amount of capital investment required, and not so much resources may go towards the ‘soft’ side of performance such as communications and people management.
But that approach has had to evolve very rapidly in recent years. People Matters asked for his take on what performance and productivity look like from the operations end of a more hands-on industry. Here are some key points he raised.
Competition drove performance before COVID
“With Malaysia being one of the key manufacturing hubs in the ASEAN region, competition has intensified for local manufacturers in recent years and has brought upon a paradigm shift in the productivity approach, moving from a focus on labour to capital expenditure programmes based on the lean management ideology.”
In a manufacturing context, productivity means being able to reduce the time and cost needed to deliver quality products from the moment of purchase. Jebsen & Jessen’s own productivity overhaul is currently most of the way through a five-year plan that began in 2018 and aims to evolve its manufacturing operations in Vietnam, Malaysia, Singapore and Indonesia to a lean system - one that reduces inventory and converts labour-intensive processes to system-oriented processes via automation.
This has involved further shifts to the workforce. Teams are trained to understand, develop, and work within the changed system. Secondly, some manual processes have been automated, meaning that workers had to be reskilled or redeployed.
Changing the performance and productivity model needs good communication
“It is important to ensure that [productivity] concepts and models are easy to understand and that employees are given the right support to successfully apply and execute them. To achieve this, clear communication is essential - especially amid the pandemic where there are fewer interactions with employees working remotely. A main focus at Jebsen & Jessen Packaging in the last few years is simplicity - to communicate simply and effectively. For example, instead of sending out lengthy emails and circulars and using legalistic and bombastic words that make things unnecessarily complicated, we would use infographics that explain things in as layman's terms as possible.”
A communication-centric approach is particularly important when making the transition to a hybrid or remote model work. Company goals and performance expectations can be more clearly laid out and communicated to individuals, and there can be greater transparency, especially around feedback on business and individual performance.
For global teams in particular, goals and objectives have to be very well communicated, and whatever matrix is used to assess the team’s performance has to be as objective as possible in the absence of face to face interactions.
In addition, motivation helps: highly motivated teams tend to perform better and overall have better alignment between broader performance strategies and individual execution.
“We understand that having great camaraderie and employee recognition are important factors for staff motivation. Strengthening bonds within the team, enhancing employee satisfaction and creating a sense of security in their value to the company, will in turn contribute greatly to better performance.”
Keeping up with technology does remain a challenge
“It is important that these performance concepts – both old and new – are implemented and executed in a way that matches the on-ground environment, and benefits employees both individually and as a whole. Comparing the old and new doesn’t mean that one is better than the other; to find the sweet spot, companies have to weigh productivity gains versus costs, before deciding on the level of investment and changes they’d like to make.”
The main performance and productivity challenge for manufacturing and similar industries is the pace of technological advancement. Keeping up with technology can often involve prohibitive capital expenditure investments, followed by the need to incorporate them into the workflow.
On the other hand, the smart use of technology for communication and feedback can improve performance noticeably. In-office workers will be familiar with many collaboration tools by now, but these extend to on-site work as well, for example a remote monitoring system that allows both the remote and on-site management and engineering teams to review machine performance and perform process troubleshooting together.