How to sustain a connected and productive company culture while managing geographically dispersed employees
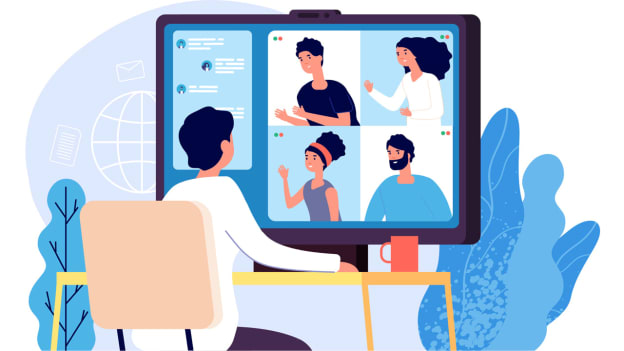
For an employee, feeling connected to an employer is everything — the ADP Research Institute found that U.S. workers who feel strongly connected to their employer are 75 times more likely to be engaged than those who do not feel connected. This connectedness also holds the key to employee engagement, and initiatives such as diversity, equity, and inclusion (DEI) can play an important role here. In fact, DEI is the no.1 priority for HR managers in 2022.
Looking at manufacturing, even within a single facility, it has largely become a completely global industry. Members of a team interact in a variety of languages and time zones. For instance, IndustrialML's partners are located on the East and West coasts of the United States—and even further afield—Japan, Singapore, India, Vietnam, and Europe.
Time zones and locales aren't the only hurdles. Every country has different local customs that must be respected, and understanding differences in workflow and holidays is critical to this. Most businesses, not just in manufacturing, use Google Hangouts or Microsoft Teams for meetings, with extra tools like Calendly to adjust for different time zones. But these tools are not suitable for all parts of a manufacturing organisation; rather, they can be inaccessible to individuals performing operations or technical work, and can limit key decision-making only to people who speak the most common language or have the most computer-heavy roles.
So how do we get over this barrier, to cultivate a comfortable working environment where there is clarity over all forms of communication? Let’s look at how manufacturing can lead the way with innovative communication methods.
Real-time language translation
Modern native language communication is beneficial to factories. Developing a software program such that it may be converted to other languages and areas without requiring engineering modifications is known as internationalisation. And localization is translating text and adding locale-specific components to internationalised software for a given location or language.
This is particularly useful because there is a lot of jargon associated with manufacturing that doesn't lend itself very well to Google Translate. A typical software application that makes it much easier to translate text for factories, even given that specific jargon, is Gettext.
This type of localization program just builds a script with a set of keywords alongside their translations, which can be worked through with a customer one time. Then, we can apply that translation to all manner of elements of the product that you provide to a customer.
Taking advantage of localization and internationalisation tools is not merely a way to increase your factory’s productivity but also an essential way to promote DEI. It opens up your project team to a broader range of stakeholders and makes it easier for office-side staff to receive and act on feedback from production floor workers.
A comprehensive communication system
The next stage is presenting all the information your stakeholders need automatically and simultaneously. For example, if you log into our platform from Japan, everything will automatically be presented in Japanese; we display our dashboards, notifications, and reports in the language of the country from which you log in, based on the IP address.
The translation tools mentioned above can be applied to speech software too. For example, an operator on the production floor could get an alert about a piece of machinery. Translated text in an audio format helps promote the safety of operators on the production floor because they get distracted by so many different visual cues in the factory. They have to monitor all their machines in places that could potentially have several trip hazards; audio communication makes it easier for them to receive critical information at the same time as office staff.
These processes can work in the other direction; capturing speech from production floor workers and returning it as translated text significantly lowers the barrier to understanding between a welding operator on a Vietnamese steel line and an executive in Miami. Properly deploying these communication and translation tools can turn digital transformation from an organisation top-down, executive-led process into one that genuinely happens collaboratively with all the diverse stakeholders in a manufacturing organisation.
These communication solutions allow organisations not to worry about team members’ understanding of specific instructions or contributions to the company. Global teams work best when their members understand where their colleagues are coming from because everyone defines themselves differently regarding their age, gender, ethnicity, etc. Utilising transparent communication systems can only positively impact the diversity and productivity of an organisation