The yin and yang of people productivity: HR contribution business leaders miss most
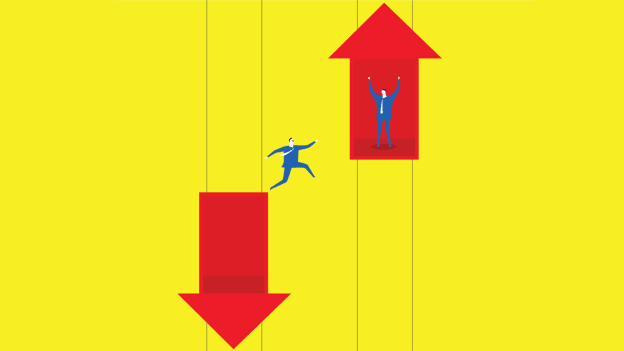
Considering that it is at least two decades since the clarion call was given for HR leaders to become business partners1, it is disappointing to find how little most business leaders think of the contribution they are getting from these Self-Appointed Partners (SAPs). For the past year, I have been probing the reasons for the dissatisfaction with a large number of business heads. Their answers, of course, differed, but if I were to extract a common theme, it was that simply understanding the business, which many CHROs consider their ultimate competency goal, was just the price of admission to the CXO table – by no means did it fulfill all the expectations the business leaders have of HR. What they were looking for were contributions only HR could make. When asked to give examples of what these unique contributions could be, the answers again varied. People productivity, however, appeared almost at the beginning of nearly every business head’s list – only to be dismissed by most of them as something HR just wasn’t equipped to deliver. Given the importance they attached to productivity, HR’s perceived (and possibly real) inability to contribute in this domain poses among the greatest threats to the relevance of HR for business.
Having identified this gap in HR capability pointed out by business heads, I pursued the topic further with several CHROs. Almost all of them confirmed that productivity occupied little of their time. Some of them were surprised it loomed so large in CEOs’ expectation-sets. Then there were those who thought the problem was for line managers to solve and that HR had contributed what it could by contractualizing a large part of the workforce. Finally, there was a significant number that was both aware of the importance of people productivity and owned it but had very incomplete and rudimentary ideas on how to go about improving it. It is to this last group that the bulk of this column is addressed. But first, we must get past the prevarications of the precariat2 purveyors.
A CHRO who does not take responsibility for and possess the skills to monitor and guide the improvement of people productivity doesnÕt deserve to be in that role
CHROs are never tired of claiming parity with CFOs and rightly so. But if they are to do so convincingly, they cannot step back from improving the productivity of the prime resource with which they deal. The CFO who disclaimed responsibility for profits and returns on capital because line managers have the prime responsibility for meeting profit targets, would not have even a day’s tenure. By the same token, the CHRO who does not take responsibility for and possess the skills to monitor and guide the improvement of people productivity doesn’t deserve to be in that role. The argument that contractualization has made improvements in people productivity irrelevant is dangerous. The large-scale denudation of the permanent workforce to which industry in India has become addicted is unfair, unsustainable, and futuristically fragile.3
The rest of this column, of course, is directed to those HR leaders who want to play a key role in people productivity improvement but face difficulties in making it happen. For them, I plan to describe some of the fundamental pillars supporting such improvement, for the want of which, the arch of productivity gain can come crashing down.
Why a 'VRS' very rarely succeeds
Have you ever wondered why, after all those drastic downsizings announced by corporates that can’t think of a better way to slake the bloodthirst of some baying shareholders, their performances continue to be in the doldrums?4 In fact, there is evidence to show their results falter even further after they slash their workforces.5 One of the reasons for this paradox is that unless there is significant slack in the system, reducing people will only leave work undone, apart from the other demoralizing effects downsizing has.6 Assuming that the work was necessary, the consequence can only be poorer quality, safety and service levels, even if some of the durable employment gets substituted by a contingent workforce.
The mistaken assumption many organizations make while slashing their workforce in the hope of cutting costs is that the work that the terminated employees were doing will vanish with them. Considering how obviously false this assumption is, it is surprising how little these organizations do to cut the work to be done or improve the efficiency with which the remaining workforce operates.
It is almost thirty years since Michael Hammer made the case for obliterating needless work instead of automating it. To the fad for automation, which Hammer criticizes, in our context, we might add the penchants for outsourcing, contractualization and the use of AI, but the message remains valid all the same. As Hammer puts it: "At the heart of reengineering is the notion of discontinuous thinking – of recognizing and breaking away from the outdated rules and fundamental assumptions that underlie operations. Unless we change these rules, we are merely rearranging the deck chairs on the Titanic. We cannot achieve breakthroughs in performance by cutting fat or automating existing processes. Rather, we must challenge old assumptions and shed the old rules that made the business underperform in the first place."7
There's always a better way
Eliminating pointless or wasteful tasks is only the beginning of the productivity improvement process. In any extant enterprise, there will always be some tasks that are essential and the productivity with which they are carried out depends on these Ms:
- Method
- Measurement
- Motivation
- Manual or Mental Skills
The first two of these appear so simple and obvious that it hardly seems worthwhile to spend any time on them. It is true that Methods of Work and Measurement of Productivity need no explanation for HR professionals. The tragedy for them and for most modern corporates arises from the fact that very few organizations any longer have the internal resources or access to reliable external expertise for undertaking these even if they wanted to.
Have you ever wondered why, after all those drastic downsizings announced by corporates that canÕt think of a better way to slake the bloodthirst of some baying shareholders, their performances continue to be in the doldrums?
Till a couple of decades ago, most large enterprises had substantive and capable Industrial Engineering departments. Admittedly, I spent a fair part of my time during the formative years of my career at the Telco (now Tata Motors) plant in Pune in conflict with worthies from Industrial Engineering. But there is no gainsaying what I learned from them and their methodical approach to measuring work and improving the efficiency with which it was carried out. Years later, when I led HR for Telco, we recruited some of the brightest people NITIE (the National Institute of Training in Industrial Engineering) and the company’s factories had to offer for building productivity planning and improvement expertise at the corporate level. It was in those years, during my regular visits to Telco’s Jamshedpur plant, that I learned the tricks of the Industrial Engineer’s trade from my friend Ravi Mukherjee (now no more), who led the department there. Over endless Charminar cigarettes and cups of tea, between the time the first shift started at 6 am and the formal agenda for my visit began a couple of hours later, Ravi would share the intricacies and problems of improving productivity while contending with a throttling incentive scheme, a strong trade union, and a frequently unstable external environment. Much of what I learned subsequently from Kaizen experts about the 'machine that changed the world' could not have been easily assimilated or implemented in the absence of such a foundation.
If today’s HR leaders were to look for similar guidance, even in those manufacturing units where Industrial Engineering continues to exist, they would find departments that are pale shadows of their former robust selves and which command little serious attention in top management deliberations. Rebuilding this capability will also not be an easy matter. The supply of smart Industrial Engineers from educational institutes has dried up – doubtless in response to dwindling demand from industry. It goes without saying that the masters of Industrial Engineering who taught us its nuances are more likely to be engaged in pushing up daisies than productivity and the Charminar (whose smoke was an essential catalyst in the transmission of tacit knowledge) is strictly prohibited in the antiseptic factory environments of today. Faced with this bleak resource horizon, some CHROs turn to manufacturing process consultants – frequently housed within the glossy confines of 'the big four'. This can at best be a temporary expedient, not just for reasons of cost but because the expertise they command in this domain is extremely shallow and operationally inexperienced. The only solution can be to reconstruct a modern avatar of the Industrial Engineering function internally, updated with appropriate learnings from the Japanese revolution in manufacturing and augmented by other proven methodologies such as TOC (Theory of Constraints).8
Eliminating pointless or wasteful tasks is only the beginning of the productivity improvement process
HR for BOP
Unlike Methods of Work and Measurement of Productivity, most HR departments do have the capability to build up the other Ms: Motivation and Manual/Mental Skills. What prevents this capacity from being used to make a major impact on productivity is the myopic concentration some HR departments have on MOP (Middle Of the Pyramid) operations. This is just one instance of the disturbing trend of focusing more and more HR effort on a smaller and smaller part of the employee population. Pious expressions of the intent to devote a fair share of HR attention to the Bottom Of the Pyramid (BOP) seem likely to materialize no quicker than it took to find King Senebkay at the bottom of another pyramid.9
After years of running engagement surveys for senior and middle-level employees, the number of corporates that have extended these to the large numbers (of direct and indirect operatives as well as contract employees) whose efforts have maximal impact on productivity, is still negligible. It is as if these surveys were Bacchic mysteries and the punishment of Pentheus10 would pulverize anyone who dared to open them up to the uninitiated. Yet this reluctance flies in the face of mounting evidence that higher levels of engagement are among the key ingredients for improving people productivity.11
Admittedly, the situation is somewhat better where skilling is concerned. Permanent employees at the BOP do get training and an opportunity to upgrade their skills. For the precariat, however, there is little beyond safety training and, even if there were, it is questionable whether such trained people would be retained long enough for the organization to benefit from the skill enhancement.
In sum, while Methods and Measurement require hard-to-acquire competencies to be re-built, Motivation and Manual/Mental Skills call for existing HR competencies to be deployed creatively to populations which are relatively neglected in most HR game-plans at present.
The great balancing act
The Yin of reducing the need for people (by eliminating wasteful work and using the four Ms to increase efficiency) must be balanced by the Yang of downsizing. Unlike the Yin of cutting the demand for manpower where, as we have seen, most HR departments either lack the key competencies or are reluctant to expend them on the BOP, they undertake the Yang of cutting headcount with unseemly relish. It is almost a rite of initiation into the big boys’ club in HR to have a couple of downsizings under your belt, like a grisly Celtic token.12 I do not gainsay the need for headcount reduction, provided it really is a last resort and accompanied by the equity-checks I have detailed in an earlier column.4 It cannot be stressed enough, however, that of the three Rs of Yang, Retrenchment is the last. It must be preceded by Re-training and Re-deployment. Every Rupee spent on these two prerequisites can save tens of Rupees in 'voluntary' retirement payments and a further ten times of that cost by avoiding the intangible damage to belongingness and morale caused by such slaughtering sprees.
Striking a real-time balance between the Yin and the Yang is as much an art as a science. Manpower Planning becomes the critical bedrock for grounding both sides of the people productivity dynamic. Its task is hugely complicated in larger corporates where different units, products and future skill requirements might demand significant intakes just when outflows are being triggered in other units by market declines and productivity gains. In coping with these complexities, the tools available for quantitative projections grow more sophisticated by the day. But they are not the last word in making accurate forecasts in uncertain and turbulent conditions. Research in recent years has yielded a wealth of insights into how forecasting capabilities can be improved. Among the more readable compendiums of both the research and the means by which the capacity for prediction can be improved is Superforecasting.13 Every manpower planner would do well to read this slim volume and even super-busy CHROs should read its eight-page appendix which contains the 'Ten Commandments for Aspiring Superforecasters'.
Make productively in India
Speaking of predictions, I don’t want to be the Laocoön of forecasters but I have to point out that the competitive advantage India enjoys internationally will be ephemeral if it continues to be based on arbitrage, as it is in several industries. The manufacturing sector is over-reliant on low-cost contract labor both directly and, even more so, though its vendors. The export-oriented service sector also relies on wage differentials between its markets and India. For obvious reasons, neither is a sustainable competitive advantage in the long-term.
In the case of manufacturing, models and methodologies for people productivity improvement (many of them pioneered by the Japanese automobile industry) already exist. In fact, several Indian corporates were well set to attaining these standards when the seemingly easy gains offered by the lower wage costs of a contingent workforce, side-tracked the effort. When they resume the more strenuous (but far healthier) journey of making permanent people productive, they will also be better positioned to implement winning strategies, such as Reverse Innovation14, which demand low-cost delivery without any sacrifice in quality or commitment.
While Methods and Measurement require hard-to-acquire competencies to be re-built, Motivation and Manual/Mental Skills call for existing HR competencies to be deployed creatively to populations which are relatively neglected in most HR game-plans
The truly golden opportunity for world-beating productivity gains, however, lies in the knowledge and service sectors, which still await their Toyota. Please don’t imagine that AI will provide the answer and that the pursuit of productivity in tech can be left to the tech mavens. That would be like imagining automation, by itself, could have solved the productivity challenge in manufacturing. In fact, US auto-makers tried precisely that response when faced with the Japanese productivity miracle decades ago – and it proved to be spectacularly unsuccessful.15 As study after study has pointed out, dramatic productivity gains demanded far more than a quick tech-fix and included a total change (at least for Western companies) in their ways of working and in the culture of the firm.16 If an Indian IT major creates the equivalent of the TPS (Toyota Production System) in the IT and tech space, it will consolidate India’s predominance in the sector for a long time to come. From that launching pad in knowledge-work productivity, the next leap could be to make radical improvements in the productivity of innovations. The organization that first makes such a jump will be assured a place in the Business Hall of Fame for all time to come.
References:
- Dave Ulrich, Human Resource Champions: The Next Agenda for Adding Value and Delivering Results, Harvard Business Review Press,1996.
- Guy Standing, The Precariat: The New Dangerous Class, Bloomsbury Academic, Reprint edition, 2016.
- Visty Banaji, Udta Udyog – Industry’s addiction to contract workers, People Matters, 15th September 2016.
- Visty Banaji, People are not beans, People Matters, 13th July 2016.
- James P Guthrie and Deepak K Datta, Dumb and Dumber: The Impact of Downsizing on Firm Performance as Moderated by Industry Conditions, Organization Science, Vol. 19, No. 1, Dec 2007.
- Rolf van Dick, Frank Drzensky and Matthias Heinz, Goodbye or Identify: Detrimental Effects of Downsizing on Identification and Survivor Performance, Frontiers in Psychology, Volume 7, Article 771, May 201
- Michael Hammer, Reengineering Work: Don’t Automate, Obliterate, Harvard Business Review, July-August, 1990.
- Eliyahu M Goldratt, Jeff Cox, and David Whitford, The Goal: A Process of Ongoing Improvement, North River Press, Revised edition, 2012.
- Stuart Jeffries, King Senebkay: how did the Egyptian pharaoh stay undiscovered for so long? The Guardian, 22 January 2014.
- Euripides, Translated by Mark Griffith, Glenn W Most, David Grene and Richmond Lattimore, Euripides V: Bacchae, Iphigenia in Aulis, The Cyclops, Rhesus, University of Chicago Press; Third edition, 2013.
- James K Harter, Frank L. Schmidt and Theodore L Hayes, Business-Unit-Level Relationship Between Employee Satisfaction, Employee Engagement, and Business Outcomes: A MetaAnalysis, Journal of Applied Psychology, Vol. 87, No. 2, 268–279, 2002.
- "Warriors proved their prowess in battle by decapitating their slain opponents. Such trophies we worn on the belt as ornaments." Patrick Harvey, The Tokens of Esteem: An Essay in Ritual Inhumanity, iUniverse, 2002.
- Philip E Tetlock and Dan Gardner, Superforecasting: The Art and Science of Prediction, Random House Books, 2016.
- Vijay Govindarajan, A Reverse-Innovation Playbook, Harvard Business Review, April 2012.
- Gwynn Guilford, GM’s decline truly began with its quest to turn people into machines, Quartz, 30 December 2018.
- John Shook, How to Change a Culture - Lessons From NUMMI, MIT Sloan Management Review, Winter 2010.